What is water jet cutting?
Water jet cutting is a technology that uses ultra-high-pressure water (ours operates at 56,000 psi) to cut a wide variety of materials. A small quantity of fine crushed garnet is added to the water stream to aid in cutting.
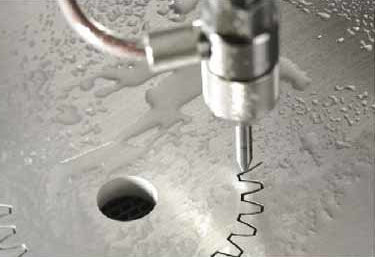
What can a water jet cut?
Virtually any material can be cut with a water jet. We frequently cut mild steel, stainless steel, aluminum, cast iron, wood, stone, concrete, ceramic tile, plastics, copper, flexible gasket materials, carbon fiber, and leather. We can even cut glass! Basically, if it can be cut, we can cut it. See our portfolio for examples.
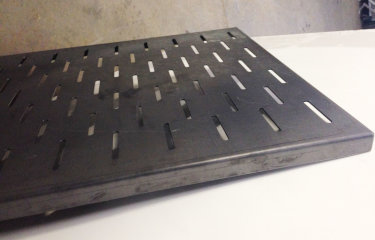
Why use a water jet?
A water jet can cut many materials that other cutting technologies cannot. Because a water jet uses water to cut instead of melting the material (e.g., laser cutting, plasma cutting, and oxy/fuel cutting), we are able to cut without imparting any appreciable heat to the material being cut. This eliminates warping due to heat, as well as eliminating the undesired material hardening and embrittlement that results from a hot cut. A water jet can cut a wide variety of materials, much thicker materials, and complex designs easier than many other cutting technologies.
What services does Liquid Impact Water Jet offer?
Liquid Impact Water Jet offers a wide range of services including water jet cutting, bend forming (using a press brake), MIG and TIG welding, CAD (computer-aided design), 3D modeling, design consultation, R&D, and prototyping. We can help you take a project from concept to completion and work with you to complete any of the steps in between.
What are our water jet’s capabilities?
We have two water jet systems and both have 60- × 120-in. cutting tables. In many cases we can cut parts larger than 60 × 120 in. We can cut up to 6-in. thick solid mild steel, up to 9-in. thick solid aluminum, and up to 4-in. thick solid stainless steel. Our minimum tolerances vary depending on the material and shape being cut. Effectively we have no minimum thickness of material we can cut; occasionally some creative fixturing may be necessary to hold exceptionally small or thin parts. We use a 0.0313-in. diameter nozzle, resulting in a very small kerf (the width of material removed in the cutting process), giving us the capability of cutting holes as small as 0.032-in. diameter. Our water jets will cut to ± 0.005-in. tolerance. We are also capable of some surface etching. Call or email us to discuss any questions you have about materials or parts you need cut, and check out our portfolio for examples of our work.
What are our bend forming (press brake) capabilities?
We have a 10-ft 190-ton press brake and an 8-ft 60-ton box and pan folder/finger brake. A variety of punch and die combinations allow us to bend a wide range of materials and thicknesses in a variety of shapes. Our punch and die library is frequently being updated. Call or email us to discuss our current capabilities.
How close can holes be to a formed bend, and what happens if holes or other cut features are too close to a bend?
Customers occasionally send parts that have holes or other cut features located near a bend line. If those parts are water jet cut and bend formed with no consideration for the proximity of holes to bend lines, the cut features will often end up deformed enough that the part is out of tolerance and unusable. Features occasionally will be drawn into a part in such a way that the part will actually move during the bend-forming process, resulting in a mis-bend and an out-of-tolerance part.
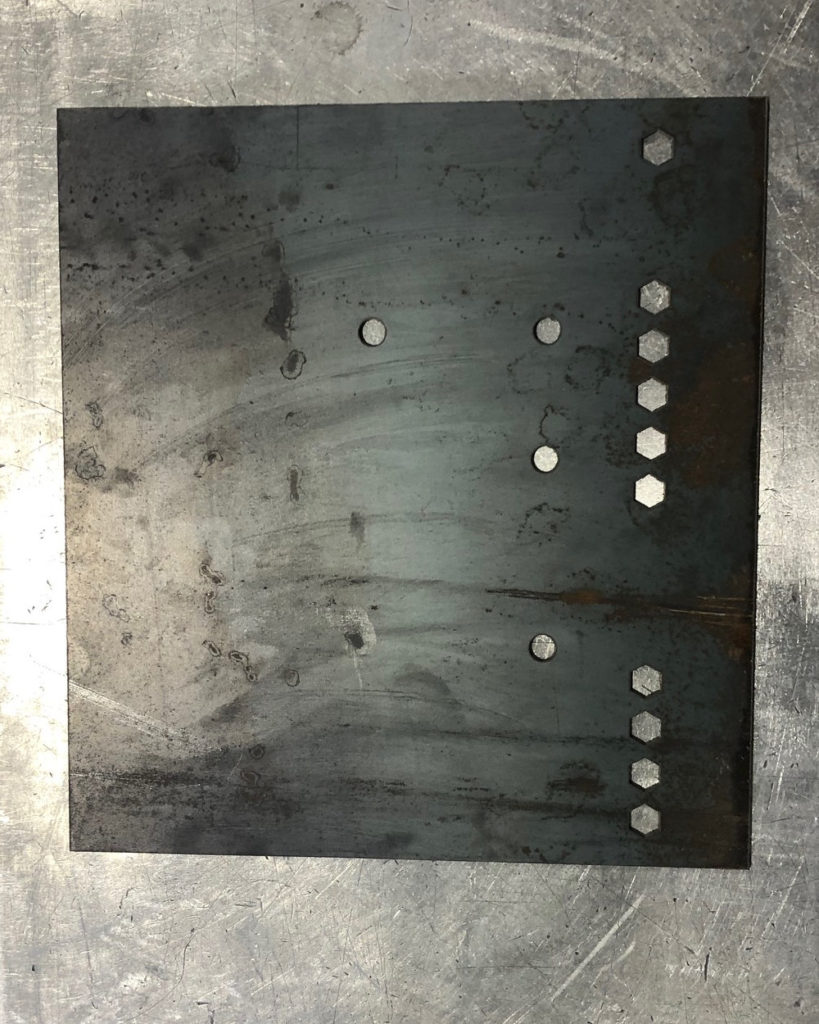
These photos show the result: the hexagonal holes are so close to the bend line that the part moved in the press brake tooling during the bend process, resulting in the holes being deformed and mislocated too near the bend-formed corner. Our solution was to first bend form the part to specification, then water jet cut the problematic hexagonal holes.
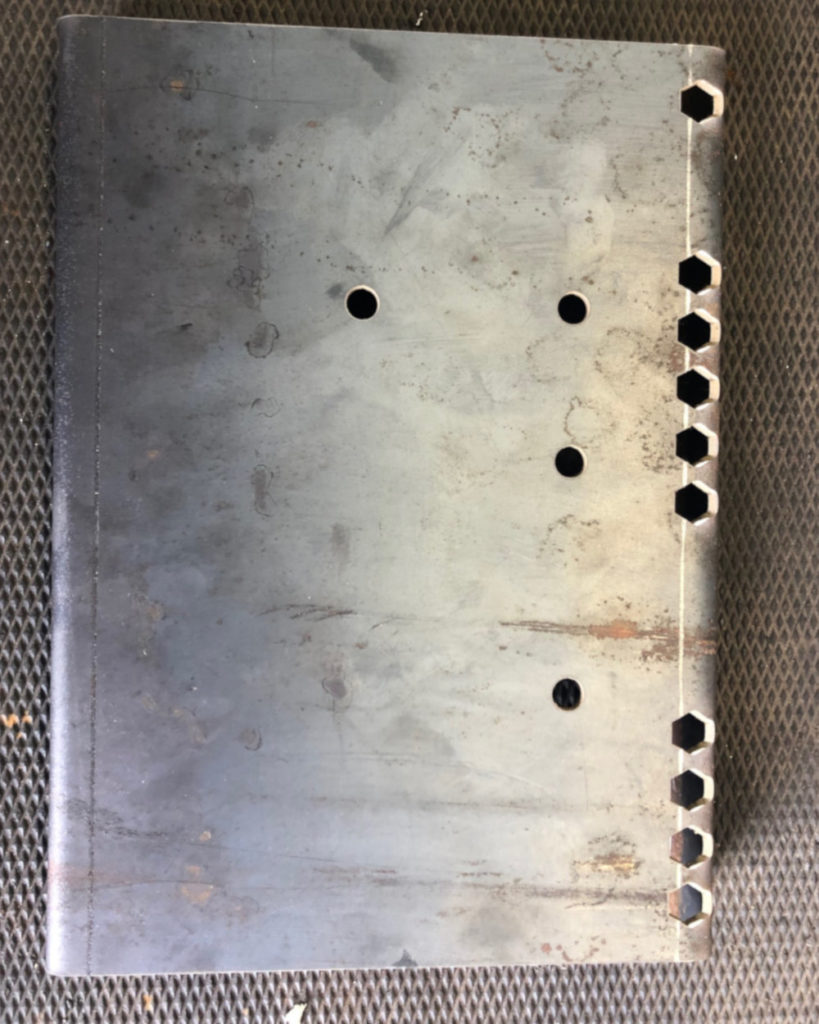
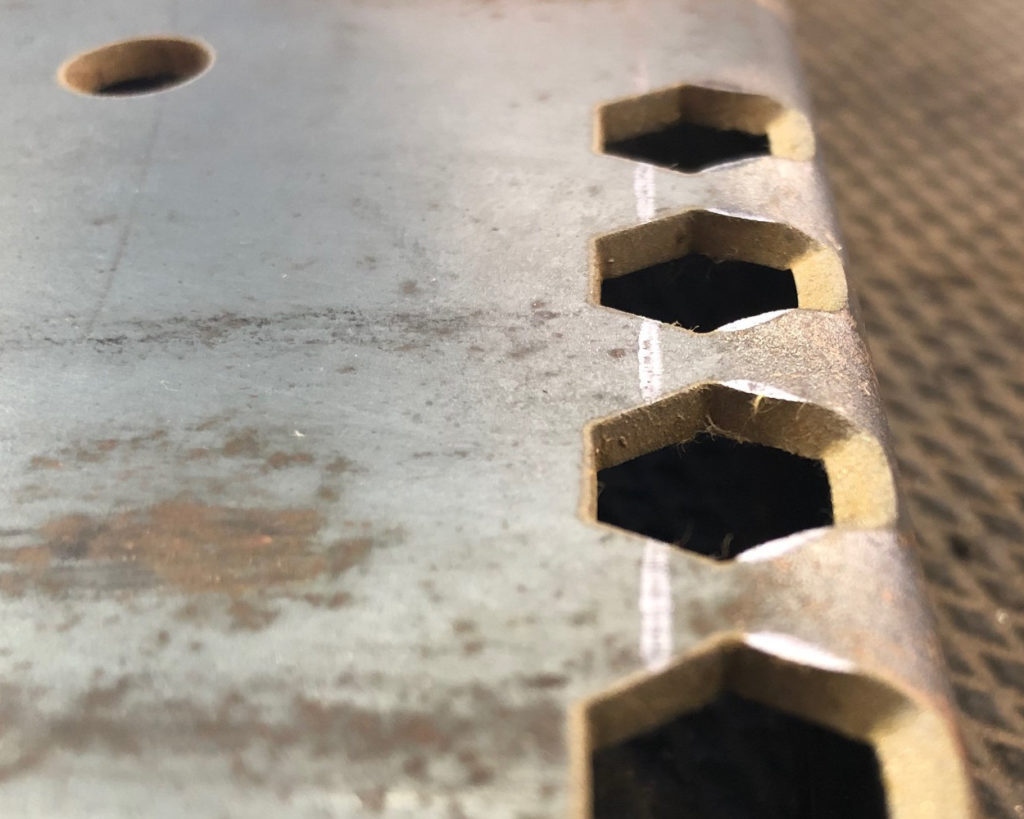
These photos show the holes in their correct placement near the bend line, with no deformation. By comparing the deformed and undeformed photos, it’s easy to see how much the part moved during the failed bend process, as well as the severe hole deformation.
While there is no single answer to how close cut features can be to a bend (each thickness and type of material has different guidelines that we follow), we look at all parts during the water jet programming process to determine whether a part will bend correctly, or whether we need to cut features after forming. Call or email us to discuss how we can meet your challenging fabrication needs.
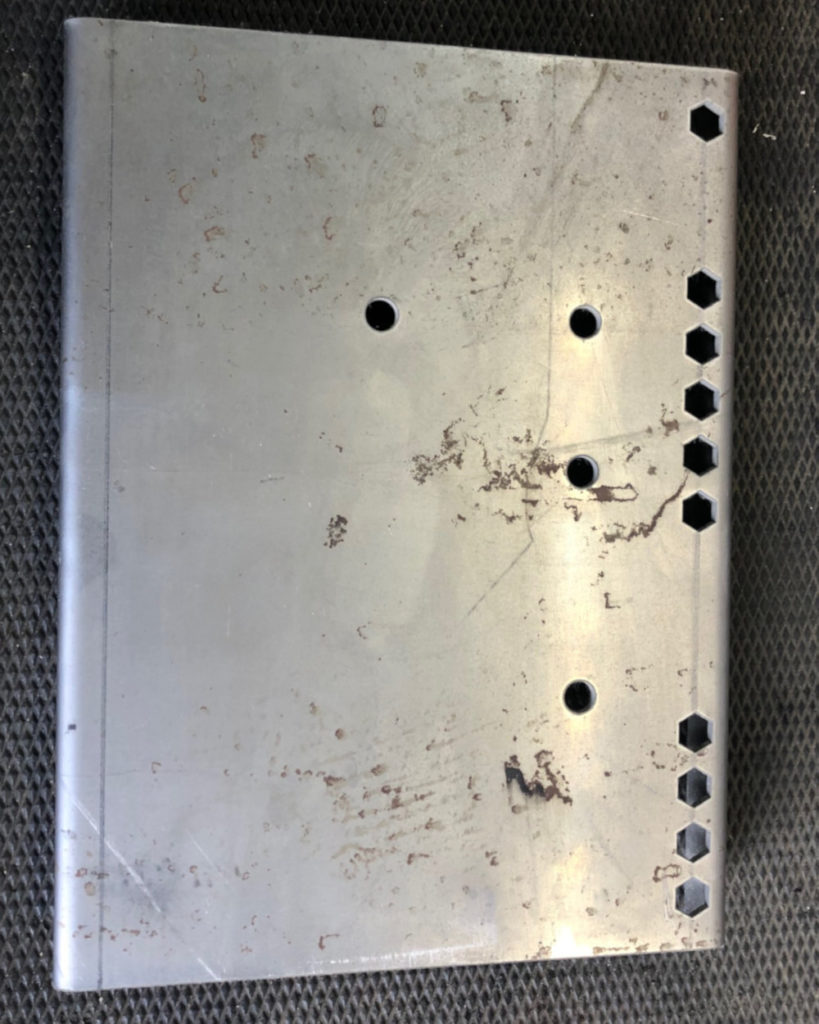
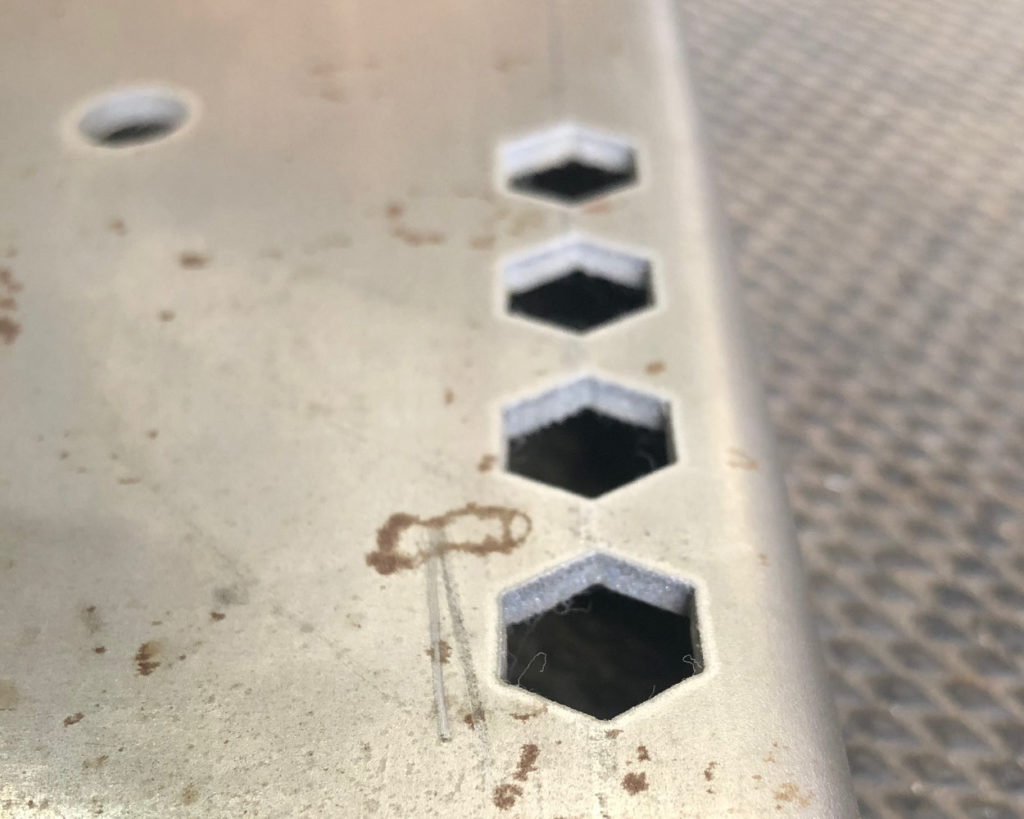
What are our welding and fabrication capabilities?
At our facility we have manual MIG and TIG welding capabilities as well as robotic MIG welding. We are experienced in welding mild steel, stainless steel, aluminum, brass, and copper. Combined, we have more than three decades of welding and fabrication experience and a very diverse body of work for many different industries and markets. Our combination of water jet, bend forming (press brake and box-and-pan folder), and welding capability allows us to complete full fabrication projects in house. Our equipment includes:
- 10- × 16-in. liquid-cooled horizontal miter-cutting bandsaw
- 14-in. liquid-cooled cold-cut miter-cutting chop saw
- manual Bridgeport mill
- manual plasma cutter
- 4-foot-wide sheet and plate shear
- various drill presses and hole cutting machines
- arbor press
- thread tapping and numerous small hand tool capabilities.
We offer full machine shop processes as well as full coating and finishing services. Call or email us to discuss our capabilities, and check out our portfolio for examples of our work.